| |
Komory wędzarnicze MAUTING UKM 200x.D
Komory wędzarnicze są produkowane w następujących wersjach:
- z indywidualnym wentylatorem usytuowanym nad każdym wózkiem
- z jednym centralnym wentylatorem
- nieprzelotowa z pojedynczymi drzwiami (prawe, lewe)
- przelotowa z dwojgiem drzwi (wjazd,wyjazd )
Komory przelotowe mogą być budowane jako tunelowe ciągi technologiczne dwu lub trzy segmentowe. Wówczas pomiędzy segmentami są stosowane drzwi dwuskrzydłowe lub gilotynowe podnoszone do góry. Przemieszczanie wózków przebiega w sposób automatyczny dzięki
zastosowaniu przenośnika hydraulicznego o konstrukcji zabezpieczającej przed skaszaniem się wózków.
Najczęściej zamawianym zestawem jest komora wędzarnicza połączona z komorą szybkiego schładzania. Taka konfiguracja skraca czas i zmniejsza koszty produkcji wyrobu dzięki eliminacji konieczności ręcznego transportu produktów do schładzania.
W zależności od potrzeb klienta komory MAUTING produkowane w różnych wersjach. Dostępne są różne pojemności nawet do 12 wózków, ustawianych w rzędach od jednego do czterech, z ogrzewaniem parowym, elektrycznym, gazowym lub olejowym, a po zastosowaniu dodatkowego wymiennika ciepła możliwe jest wędzenie dymem zimnym w zakresie temperatur 12°C-35°C.
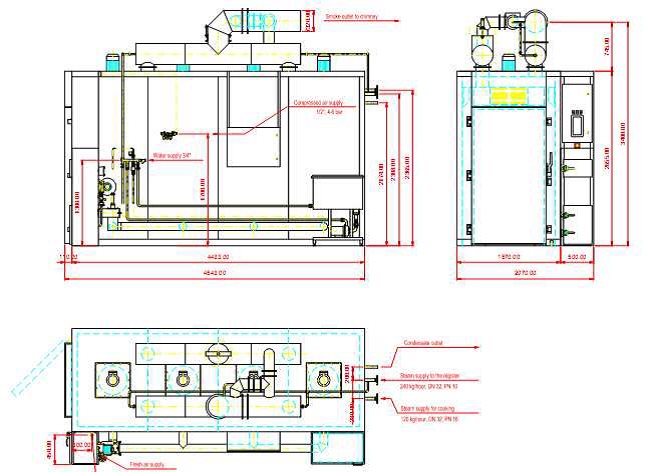
Komora wędzarnicza 4 wózkowa 1 rzędowa w wersji z wentylatorem nad każdym wózkiem
Charakterystyka
- Automatyczne komory wędzarnicze firmy MAUTING przeznaczone są do wędzenia oraz obróbki termicznej mięsa i produktów mięsnych. Zapewniają czerwienienie, suszenie, wędzenie i gotowanie podczas jednego, nieprzerwanego procesu technologicznego bez dodatkowej ingerencji w ten proces.
- Wyposażone są w specjalną, wzmocnioną podłogę przystosowaną do standardowych wózków o wymiarach 1x1x2m (szerokość x głębokość x wysokość)
- Maksymalna temperatura podczas procesu obróbki termicznej wynosi 110°C, przy wilgotności względnej powietrza 98%.
Budowa komory wędzarniczej UKM 200x.D
- UKM 200x.D – x-wózkowa jednorzędowa (wózki ustawione są w jednym szeregu jeden za
drugim)
- korpus komory wykonany z najwyższej jakości stali nierdzewnej: na zewnątrz stal 1.4301,
wewnątrz stal 1.4571 z domieszką tytanu
- panele sufitowe i ścienne izolowane wełną mineralną o grubości 80 mm
- najwyższa jakość wykonania konstrukcji, izolacji i uszczelnienia paneli umożliwia utrzymanie długoletniej trwałości urządzenia oraz maksymalnej oszczędności energii
- konstrukcja ścian i drzwi zabezpiecza przed powstawaniem mostków termicznych
- podłoga komory wykonana jest ze stali nierdzewnej 1.4303 i jest wzmocniona wspornikami
zabezpieczającymi przed powstawaniem odkształceń podczas załadunku nawet maksymalnie
obciążonymi wózkami; podłoga posiada nachylenie ułatwiające załadunek, otwór do
wyrównywania ciśnienia, odprowadzenia kondensatu i wody
- jednoskrzydłowe drzwi wykonane ze stali nierdzewnej (na zewnątrz stal 1.4301, wewnątrz stal 1.4571) izolowane wełną mineralną o grubości 100mm
- drzwi prawostronne , lewostronne lub gilotynowe
- istnieje możliwość zainstalowania dodatkowych drzwi w ścianie tylnej, dzięki czemu poprawia się funkcjonalność komory, skraca czas wymiany produktu w komorze lub uzyskuje ciąg technologiczny z komorą szybkiego schładzania (w przypadku, gdy produkt jest poddawany procesowi szybkiego schładzania)
- wewnątrz komory są prowadnice wózków
- komora zawiera system czujników przeznaczonych do pomiaru temperatury, wilgotności oraz ochrony przed przegrzaniem
- komora zawiera czujnik pomiaru temperatury rdzenia produktu, co pozwala na utrzymanie stałej różnicy temperatur wewnątrz produktu i na jego powierzchni
- automatyczny generator dymu na zrębki wędzarnicze
- generator dymu i pulpit sterowniczy montowane z prawej lub z lewej strony komory; możliwość zamontowania generatora dymu i pulpitu w dowolnym miejscu w odległości do 15 m od komory
- wymuszony wyciąg zużytej mieszaniny powietrza i dymu oraz pobór świeżego powietrza,
wykonany w całości ze stali nierdzewnej z systemem zaworów pneumatycznych, bez
przewodu kominowego (opcja dodatkowa)
- automatyczny system mycia komory, generatora dymu, przewodów doprowadzających oraz odprowadzających mieszaninę dymu i powietrza
- komora wyposażona w filtr do oczyszczania dostarczanego powietrza
- materiały użyte do wykonania odpowiadają wysokim wymaganiom eksploatacyjnym zapewniając długą i bezawaryjną eksploatację
- wymiennik parowy wykonany ze stali nierdzewnej
System cyrkulacji
- komora może być wyposażona w wentylatory umieszczone nad każdym wózkiem lub w jeden centralny wentylator w zależności od potrzeb i decyzji klienta
- dwie prędkości obrotowe silnika elektrycznego zapewniają możliwość zmiany prędkości wyciągu mieszaniny powietrza i dymu w zależności od fazy programu i przebiegu procesu
technologicznego
- wirnik wentylatora wykonany jest ze stali nierdzewnej i pokryty specjalną powłoką
zabezpieczającą przed przyleganiem osadów, uniemożliwiając powstawanie wibracji, a w
konsekwencji znacznie przedłuża żywotność urządzenia
- dokładnie zaprojektowany system przewodów powietrznych oraz dysz zapewnia bardzo
precyzyjną, równomierną cyrkulację mieszaniny dymu z powietrzem wewnątrz komory, dając równomierny rozkład temperatury (maksymalna różnica w przeciwległych punktach komory nie może przekroczyć 0,7ºC )
- precyzyjna cyrkulacja powietrza, równomierny rozkład temperatury i wilgotności w każdym punkcie komory pozwala w najwyższym stopniu zoptymalizować proces obróbki cieplnej i zminimalizować straty wagi gotowych produktów
- system doprowadzania świeżego powietrza i odprowadzania zużytej mieszaniny dymu jest
wykonany ze stali nierdzewnej 1.4301 i umieszczony na suficie komory
- elektryczne sterowanie pneumatycznych klap i zaworów
- system klap i zaworów wyrównujący ciśnienie powietrza wewnątrz komory do ciśnienia atmosferycznego
Wycinki z symulacji komputerowej przedstawiają cyrkulację powietrza w komorze. Kolory oznaczają prędkość obiegu powietrza w m/s.
Cyrkulacja (50/50) przedstawia obieg powietrza w komorze z wentylatorem
umieszczonym nad każdym wózkiem. W takim przypadku jeżeli dodatkowo zastosujemy specjalny system klap i zaworów wymuszających obieg powietrza w komorze , uzyskamy możliwość wędzenia produktów na siatkach oddalonych od siebie co 20cm.
Pozostałe wycinki przedstawiają cyrkulację powietrza w komorze w wersji z
jednym centralnym wentylatorem. Takie rozwiązanie pozwala wędzić na siatkach o rozstawie co 10cm. Dodatkowo można pozostawić mniej wolnej przestrzeni między produktami, co jeszcze bardziej podnosi wydajność komory.
Niezależnie od rodzaju zastosowanej cyrkulacji, system obiegu powietrza gwarantuje otrzymanie jednakowego produktu w optymalnym czasie, niezależnie od wielkości komory i położenia wózka w komorze.
Generator dymu
Jest generatorem typu zamkniętego na zrębki wędzarnicze z twardego drewna liściastego. Pracownik nie ma możliwości ingerencji w komorę tlenia podczas pracy generatora. Proces przebiega automatycznie, jest programowany i nadzorowany za pomocą mikroprocesorowego pulpitu sterowniczego firmy ADITEC. System czujników monitoruje poziom zrębków w komorze zasypowej, temperaturę tlenia i temperaturę dymu. System pneumatycznych zaworów reguluje przepływ powietrza. Przy przekroczeniu jakichkolwiek maksymalnych wielkości zadanych temperatur dymogenerator automatycznie wygasi tlenie zrębków poprzez zmianę przepływu powietrza w komorze tlenia lub poprzez natrysk wody. Oprócz generatorów na zrębki wędzarnicze komora może być wyposażona w generator frakcyjny, parowy lub aplikator ciekłego dymu.
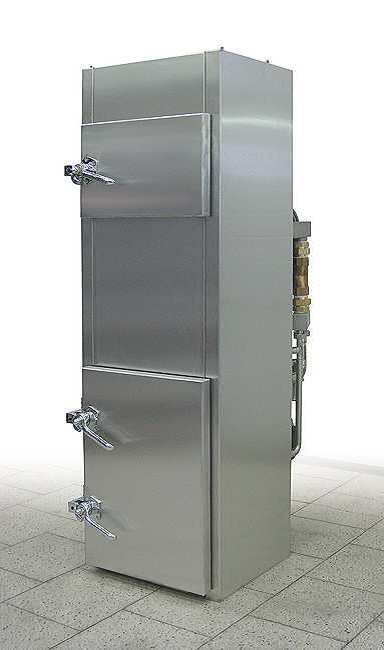
Na zrębki
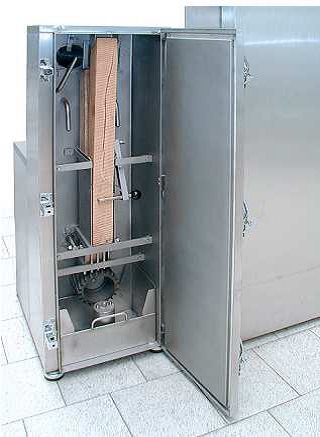
Cierny
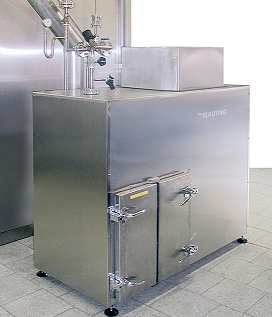
Parowy
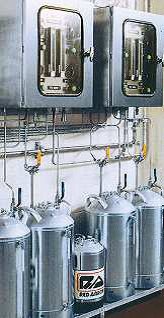
Aplikator ciekłego dymu
System sterowania
Pulpit sterowniczy ADITEC MIC 2420 jest wbudowany w nierdzewną szafę zamontowaną nad generatorem dymu. Pozwala na śledzenie bieżących i zaprogramowanych parametrów przebiegu procesu technologicznego, które widoczne są na kolorowym wyświetlaczu.
Na wyświetlaczu widoczna jest temperatura wewnątrz komory, temperatura wewnątrz produktu wraz z parametrem Δt, wilgotność względną, czas, numer programu oraz aktualnego kroku.
System sterujący odpowiada za:
- Regulację temperatury wewnątrz komory
- Utrzymanie odpowiedniej wilgotności
- Kontrolę procesu gotowania zgodnie z zadanym Δt
- Sterowanie pracą dymogeneratora
- Proces automatycznego mycia
- Prędkość obrotową wentylatorów
- Pracę klap, zaworów i systemu pneumatycznego
- Uruchomienie dodatkowych urządzeń takich jak: natrysk wody, chłodzenie, automatyczne otwieranie drzwi, itp.
Standardowy zestaw etapów procesu technologicznego to: czerwienienie, suszenie, wędzenie i gotowanie. Kombinacja czasów poszczególnych kroków obróbki termicznej odbywa się tak, aby cały proces technologiczny był zakończony w optymalnym czasie i przy minimalnych stratach gotowego produktu. W celu optymalizacji strat produktu wykorzystuje się sposób ogrzewania oparty na różnicy Δt. System sterowania pozwala na tworzenie indywidualnych programów produkcyjnych, a sterownik ma możliwość zaprogramowania 99 programów, przy czym każdy z nich może realizować do 20 różnych kroków.
Programowanie sterownika odbywa się w prosty i intuicyjny sposób, a wszelkie zmiany parametrów poszczególnych kroków w celu zoptymalizowania procesu technologicznego można dokonywać szybko i łatwo. Sterownik sygnalizuje optycznie i akustycznie koniec programu, a także optycznie sygnalizuje końce poszczególnych kroków programu. Seryjnie montowany interfejs RS232 pozwala na połączenie systemu sterowania z komputerem technologa dla archiwizacji danych dotyczących przebiegu programu i w celu dokonywania zmian w programach.
Firma MAUTING dostarcza oprogramowanie o nazwie MautingNet, przeznaczone dla systemu operacyjnego Windows, składające się z dwóch elementów: programu do zbierania danych i programu do ich przetwarzania.
|